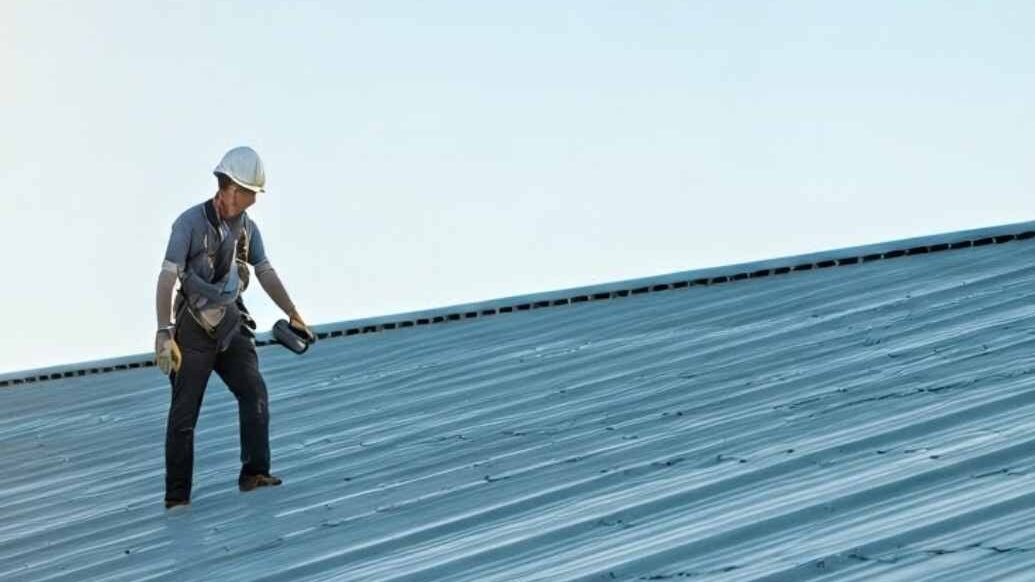
Key Highlights
- Regular metal roof inspections are vital for maintaining a durable and long-lasting roofing system.
- By identifying and addressing issues early on, you can prevent costly repairs and extend the lifespan of your metal roof.
- A comprehensive inspection involves examining the roof, flashing, gutters, and downspouts, and checking for signs of rust, corrosion, leaks, or damage.
- Safety should always be a top priority during any roof inspection.
- Engaging a qualified roofing professional for thorough inspections and maintenance is recommended to ensure optimal roof performance.
Introduction
Metal roofing is a popular choice for both residential and commercial buildings due to its durability and longevity. However, like all roofing materials, periodic maintenance and inspections are crucial to ensure optimal performance and longevity. Regular roof inspections can help identify potential problems early on, preventing costly repairs and extending the life of the roof. This blog post will serve as an essential metal roof inspection checklist, guiding homeowners and property managers on what to look for and when to seek professional roofing assistance.
Why Regular Metal Roof Inspections are Crucial

Regular metal roof inspections are essential for a number of reasons. Primarily, inspections help identify potential issues in their initial stages. Just like any other part of a building, roofs are subject to wear and tear over time. Exposure to harsh weather conditions, debris impact, and natural aging can lead to various issues that compromise the roof’s integrity. Early detection often translates to simpler and less expensive repairs.
Moreover, regular inspections can extend the lifespan of your metal roof significantly. By addressing minor issues promptly, you can prevent them from escalating into major problems that may require extensive and costly repairs or even a complete roof replacement.
Identifying Potential Issues Early
A thorough roof inspection involves a visual assessment of the entire roof surface, checking for signs of wear, damage, or aging. This includes examining the condition of the metal panels, looking for dents, scratches, loose or missing fasteners, and signs of rust or corrosion. Pay close attention to areas where different roof planes intersect, such as valleys and ridges, as these areas tend to be more prone to leaks.
Inspecting for signs of water damage is crucial during a roof inspection. Check for water stains on the underside of the roof deck, which is visible from the attic. Look for signs of moisture, such as mold, mildew, or discoloration in the insulation. Any signs of water damage should be addressed immediately to prevent further damage to the roof structure and the interior of the building.
Remember, addressing these issues in their early stages can often be accomplished with simple repairs or maintenance tasks. Ignoring them can lead to more significant problems down the line, resulting in costly repairs or even premature roof replacement.
Extending the Lifespan of Your Metal Roof
Extending the lifespan of your metal roof requires proactive maintenance and timely repairs. One of the most critical aspects is ensuring proper drainage. Inspect the gutters and downspouts regularly, removing any debris or clogs that could obstruct water flow. Proper drainage prevents water from pooling on the roof, which can lead to rust, corrosion, and leaks.
Another essential aspect of metal roof maintenance is keeping the roof surface clean. Over time, dirt, debris, algae, and moss can accumulate on the metal panels, trapping moisture and accelerating the deterioration process. Cleaning the roof regularly with a gentle pressure washer and appropriate cleaning solutions can help prevent these issues.
Following the manufacturer’s recommendations for maintenance and using compatible sealants and coatings will ensure your metal roof stays in optimal condition for years to come.
Preparing for a Metal Roof Inspection
Before you begin the metal roof inspection, gather the necessary tools and equipment to ensure a safe and efficient process. This may include a sturdy ladder, safety harness, gloves, appropriate footwear, a flashlight, binoculars, a measuring tape, and a camera to document any findings.
Clear the work area of any obstacles or debris that could pose a tripping hazard. Consider the weather conditions, avoiding inspections during rain, snow, or high winds. If you encounter any unsafe conditions, it’s always best to err on the side of caution and postpone the inspection.
Tools and Equipment Needed
Having the right inspection tools and safety equipment is crucial for a successful and safe roof inspection. Your safety gear should include a sturdy ladder that extends beyond the roof edge, a safety harness with a roof anchor point, non-slip gloves for secure handling, and appropriate footwear with good traction.
In addition to safety equipment, gather the necessary tools for a thorough inspection. These may include a flashlight or headlamp for illuminating dark areas, binoculars for close-up inspections from a distance, a measuring tape for assessing panel dimensions and identifying areas of concern, and a camera or smartphone to document any findings with pictures or videos.
Having a checklist on hand is useful for staying organized and ensuring that all critical areas are inspected. The checklist should include sections for inspecting the roof’s surface, flashing, gutters, downspouts, and any penetrations or roof protrusions.
Safety Measures to Consider
Safety should always be the top priority when conducting a metal roof inspection, as working at heights poses significant risks. Avoid inspecting the roof during inclement weather conditions, such as rain, snow, or high winds, as these conditions can make the roof slippery and increase the risk of falls.
Before accessing the roof, ensure the ladder is placed on a stable and level surface. It is recommended to have a helper steady the ladder while you climb. When working on the roof, wear a safety harness securely attached to a designated anchor point. Non-slip gloves and footwear with good traction are also essential for maintaining a firm grip and preventing slips.
Inspect the roof cautiously, avoiding stepping on wet or moss-covered areas. Never attempt to walk on a roof that is visibly damaged or structurally compromised. If you encounter any unsafe conditions during the inspection, descend from the roof immediately and consult a qualified roofing professional for further assessment and repairs.
Key Areas to Inspect on a Metal Roof
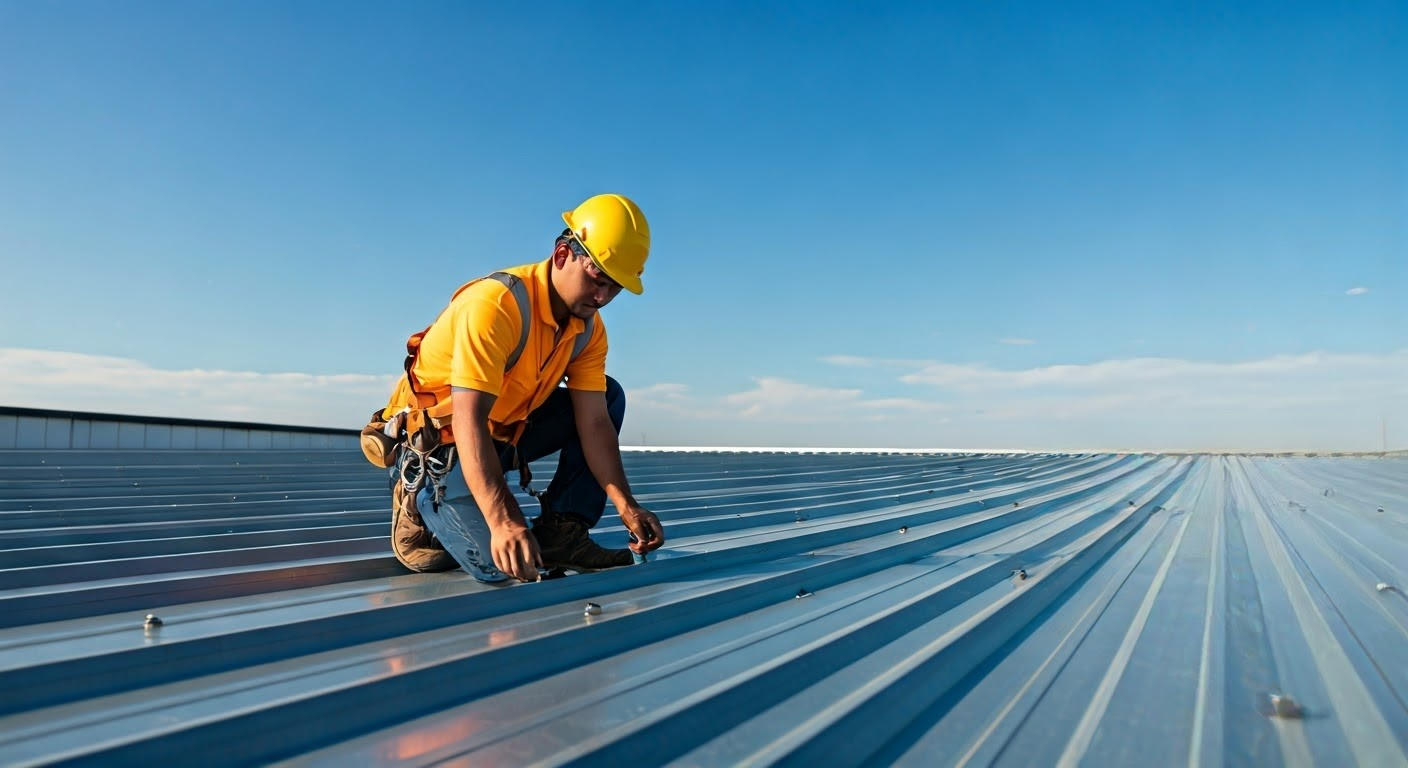
When inspecting a metal roof, certain areas require particular attention due to their susceptibility to wear, tear, and potential issues. These key areas include the metal panels themselves, flashing details, the gutter system, and any roof penetrations or protrusions, such as chimneys, vents, or skylights.
For instance, begin by visually inspecting the metal panels for any signs of rust, corrosion, dents, scratches, or loose or missing fasteners. Examine the flashing details around chimneys, vents, skylights, and other roof penetrations, ensuring they are properly sealed and free from any gaps or damage.
Checking for Rust and Corrosion
Rust and corrosion are common issues that can affect metal roofs over time, compromising the roof’s structural integrity and leading to leaks if left unaddressed. Carefully inspect the metal panels, paying close attention to areas where the coating may have worn away, exposing the underlying metal to the elements.
Look for rust spots, which typically appear as reddish-brown discoloration on the surface. Use a screwdriver or other sharp object to gently probe any rust spots to determine the extent of the damage. If the rust is superficial, it can usually be treated with a rust-inhibiting primer and a compatible topcoat.
However, if the corrosion is severe and has eaten through the metal, panel replacement may be necessary. Consult a qualified roofing professional to assess the severity of the rust and corrosion and recommend the appropriate course of action.
Inspecting Seals and Fasteners
Properly sealed seams and secure fasteners are crucial for preventing water intrusion and maintaining the integrity of your metal roof. Inspect all seams, joints, and flashing details, paying attention to the condition of the sealant. Over time, sealants can dry out, crack, or pull away, compromising the roof’s watertightness.
Examine the fasteners, typically screws or clips, that secure the metal panels to the roof deck. Ensure they are snug and free from rust or corrosion. Loose or damaged fasteners can allow the panels to lift, creating gaps that make the roof vulnerable to wind uplift and water intrusion.
If you notice any signs of moisture penetration around seals or fasteners, it is crucial to address the issue promptly to prevent further damage to the roof and the building’s interior.
Evaluating the Roof’s Structural Integrity
While metal roofing panels are generally durable, it is crucial to evaluate the structural integrity of the entire roof system during an inspection. The roof structure, including the rafters, trusses, and decking, provides essential support for the metal panels.
Inspect the roof deck for signs of sagging, deflection, or deterioration. Check the attic, if accessible, for any signs of water damage or structural issues that may originate from the roof. Look for cracks, rot, or insect infestation in the rafters or trusses.
If you notice any signs of structural damage, it is crucial to contact a qualified structural engineer or roofing contractor to assess the situation and recommend appropriate repairs.
Common Problems Found During Metal Roof Inspections
During metal roof inspections, certain problems are more prevalent than others, often arising from wear and tear, weather exposure, or improper installation. These common issues can range in severity from minor cosmetic imperfections to major structural problems requiring immediate attention.
Some frequent problems include leaks and water damage, often stemming from damaged flashing, compromised seals, or deteriorating roofing materials. Additionally, loose or missing panels, often caused by high winds or improper installation, are commonly encountered.
Leaks and Water Damage
Roof leaks are among the most common issues encountered during metal roof inspections. Water intrusion can occur due to various reasons, including damaged or deteriorated flashing, compromised seals around penetrations, or even small holes or gaps in the metal panels.
Look for water stains on the underside of the roof deck, visible from the attic. Water stains often appear as discolored areas, which may be accompanied by mold or mildew growth. Check for signs of water damage in the insulation, such as dampness or a musty odor.
Trace the water stains back to their source, which may involve inspecting the roof from the exterior as well. Identifying the root cause of the leak is essential for effective repairs and preventing future water damage.
Loose or Missing Panels
High winds, improper installation, or even normal wear and tear can cause metal roof panels to become loose or detached from the roof deck. This issue can create significant vulnerabilities, allowing wind and water to infiltrate the roof system.
Inspect all metal panels, paying close attention to their attachment points and ensuring they are securely fastened to the roof deck. Look for any signs of movement, lifting, or gaps between the panels.
If you encounter any loose or missing panels, it is crucial to address the issue promptly.
Conclusion
Regular metal roof inspections are paramount for the longevity and performance of your roofing system. By identifying issues early on and ensuring proper maintenance, you can extend the lifespan of your metal roof. From checking for rust and corrosion to evaluating structural integrity, a thorough inspection covers key areas that could potentially lead to costly repairs if left unchecked. Remember, proactive maintenance is key to preventing leaks, water damage, and other common issues. Stay ahead by scheduling routine inspections and prioritizing the health of your metal roof. If you need assistance with your metal roof inspection or maintenance, contact us today for expert guidance.
At “Metal Roof Mobile AL”, we ensure our clients receive the best possible outcomes. Our commitment to quality workmanship and customer satisfaction is unwavering, making us the top choice for residential Roofing services in our community.
Frequently Asked Questions
How often should a metal roof be inspected?
While specific standards of practice vary, a metal roof should ideally be inspected annually to ensure its durability and longevity. This helps identify any potential issues early, contributing significantly to the roof’s lifespan.
Can I perform a metal roof inspection myself?
While a homeowner can perform a basic roof inspection, working at heights involves risks. Familiarity with roofing materials, an understanding of safety measures, and access to proper inspection tools are crucial. If unsure, consult a professional roofing contractor.